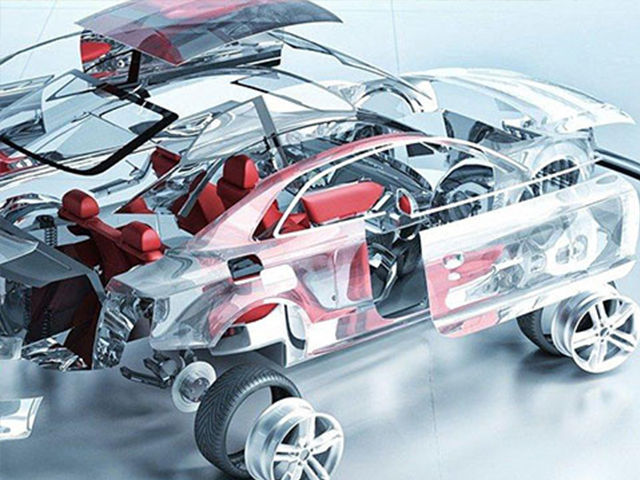
The generation of sprues is a common problem during the injection molding process in the automotive parts industry. These sprues not only take up space but also cause waste to resource utilization and the environment. To solve this problem, low-speed crushing and recycling machines came into being.
Low-speed crushing and recycling machine is a kind of high-efficiency equipment designed specifically for the automobile parts industry, which can efficiently crush PVC/PP/ABS/TPR/TPU and other sprues, sieve out the dust and automatic mix of a fixed ratio, and then directly transported to the screw immediately used to reduce the cost of raw material purchases, improve production efficiency, reduce manpower costs, and improve the stability of the quality of the product and reliability.
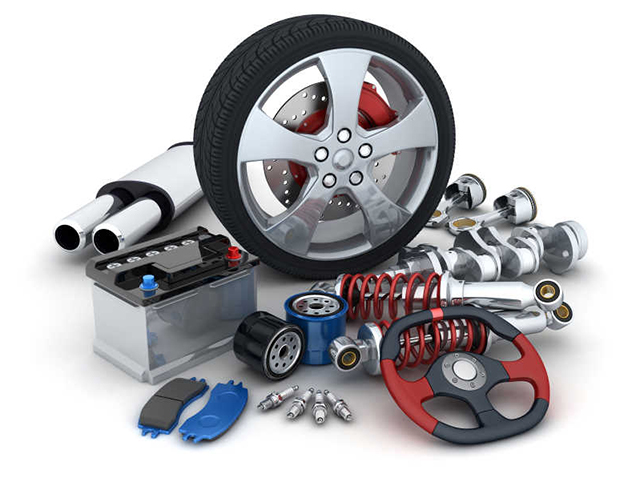
Client Testimonials
More than 60% durable compared to the same period of time, saving effort and money
Featured Products
No noise: the noise is as low as 50 decibels, reducing noise pollution.
Easy to clean: the crusher adopts a V-shaped diagonal cutting design
Ultra-durable: service life up to 5~20 years.
High return: almost no after-sale maintenance cost.
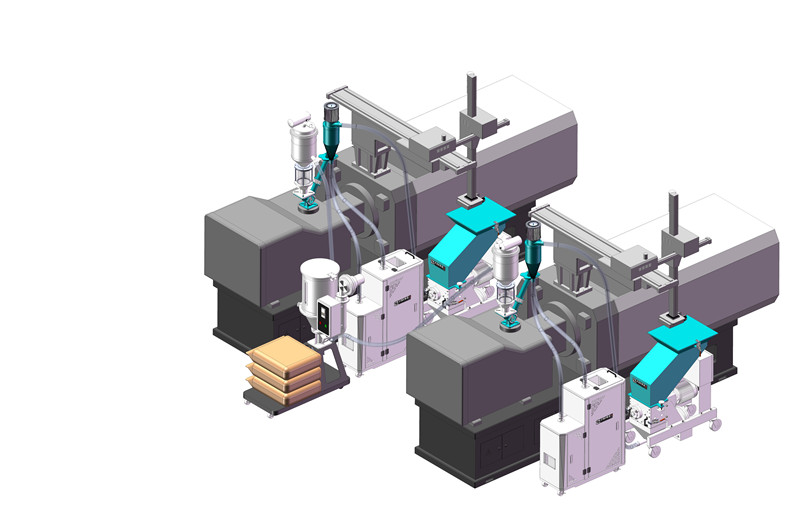
ORTUNE GLOBAL 500 CERTIFICATION
Good quality comes from every detail
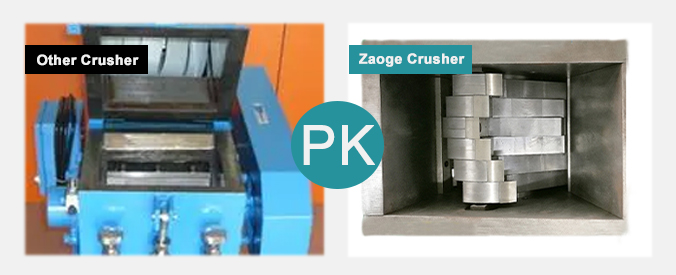
Low-Speed Crusher · Crushing Chamber
The open structure design of the crushing chamber allows for easy and quick color and material changeovers, reducing downtime and improving production efficiency.
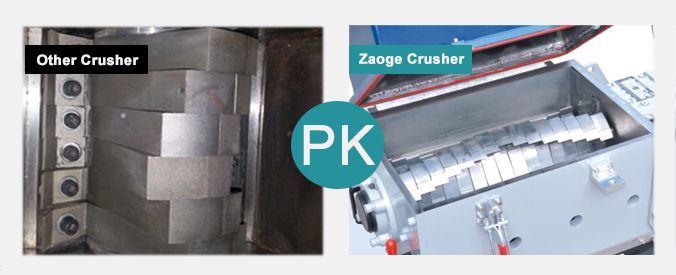
Low-Speed Crusher · Imported Blade Material
The blades are made of Japanese NACHI material, known for its hardness and wear resistance. The V-shaped design of the blades ensures quieter cutting and less generation of powder.
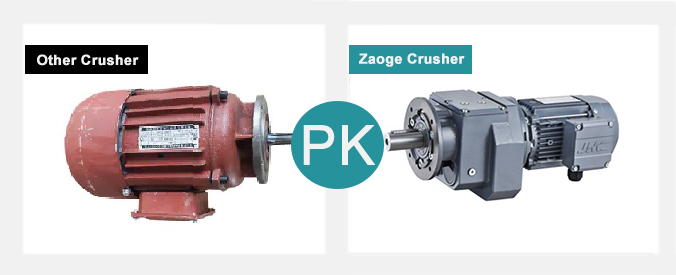
Low-Speed Crusher · Motor Transmission
Taiwan Dongyuan/Siemens reduction motors offer greater torque and lower energy consumption, resulting in cost savings and reduced environmental impact.
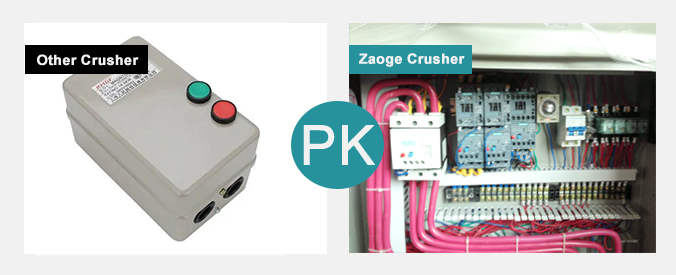
Low-Speed Crusher · Control Box
Utilizing Taiwan Dongyuan/Siemens with a dual-group design, providing more reliable control and higher safety.
FAQ
We are a Manufacturer located in Dongguan, China. Specialized in, it has been focusing on the research, development, production, and sales of high-quality, high-performance rubber and plastic environmental protection automation equipment. for more than 43 years, have thousands of customer cases, welcome for factory inspection.
MOQ is 1 pcs.
Sample is available for customer to check the quality before bulk order.
Our factory mainly produces plastic granulator products (such as Plastic Shredder, plastic dryer, Plastic chiller, etc.), and we can also customize other types of products according to customer needs.
Yes, we provide Non-standard customization service. We have a professional R&D team and production equipment, and can design and manufacture products according to customer needs.
Our factory has advanced technical equipment and efficient production lines, which can meet the needs of large-scale production. You can consult us for the specific production capacity, and we will evaluate and arrange according to your needs.
We attach great importance to product quality, and our factory strictly abides by the relevant quality management system and has passed ISO certification. During the production process, we will conduct multiple quality inspections to ensure that the products meet or exceed customer requirements and standards.
For samples, the lead time is about 7 days. For mass production, the lead time is 20-30 days after receiving the deposit payment. The lead times become effective when (1) we have received your deposit, and (2) we have your final approval for your products. If our lead times do not work with your deadline, please go over your requirements with your sale. In all cases we will try to accommodate your needs. In most cases we are able to do so.
You can make the payment to our bank account, Western Union or PayPal:
30% deposit in advance, 70% balance against the copy of B/L.
Yes, we can provide most documentation including Certificates of Analysis / Conformance; Insurance; Origin, and other export documents where required.
The shredder phase helps to protect the granulator by reducing the load during regrind once it is pre-shredded. It is best to use a shredder for heavy duty materials at a high volume. Shredder type may vary depending on the material type (e.g. single-shaft vs. multi-shaft). Most shredders can be used inline for continuous shredding.
Keeping you granulators and shredders maintained is very important. Be sure to regularly sharpen and replace knives when necessary. Dull knives produce less quality regrind and increase vibrations, which may cause more frequent maintenance.
ORTUNE GLOBAL 500 CERTIFICATION
Rubber products produced using the ZAOGE Rubber Environmental Utilization System are sold in over 100 countries worldwide.